Maximizing Your Welding WPS: Strategies for Improved Efficiency and Effectiveness
Maximizing Your Welding WPS: Strategies for Improved Efficiency and Effectiveness
Blog Article
Getting Welding Excellence: Revealing the Secrets of WPS Application and Optimization
In the realm of welding, achieving quality is a search that pivots on the careful execution and optimization of Welding Treatment Requirements (WPS) These foundational documents work as the backbone of welding procedures, dictating the criteria and procedures required for creating high-quality welds constantly. Nevertheless, the tricks to unlocking the full possibility of WPS lie not only in recognizing its value yet additionally in mastering the ins and outs of its application and optimization. By delving right into the crucial elements, techniques, obstacles, and ideal methods related to WPS, a world of welding quality awaits those who are ready to explore its midsts.
Importance of WPS in Welding
The Importance of Welding Treatment Specifications (WPS) in the welding market can not be overstated, acting as the backbone for ensuring uniformity, high quality, and security in welding operations. A WPS supplies thorough instructions on just how welding is to be executed, including essential variables such as products, welding procedures, joint design, filler steels, interpass and preheat temperatures, welding currents, voltages, traveling speeds, and more. By sticking to a distinct WPS, welders can keep harmony in their job, causing regular weld top quality throughout various jobs.
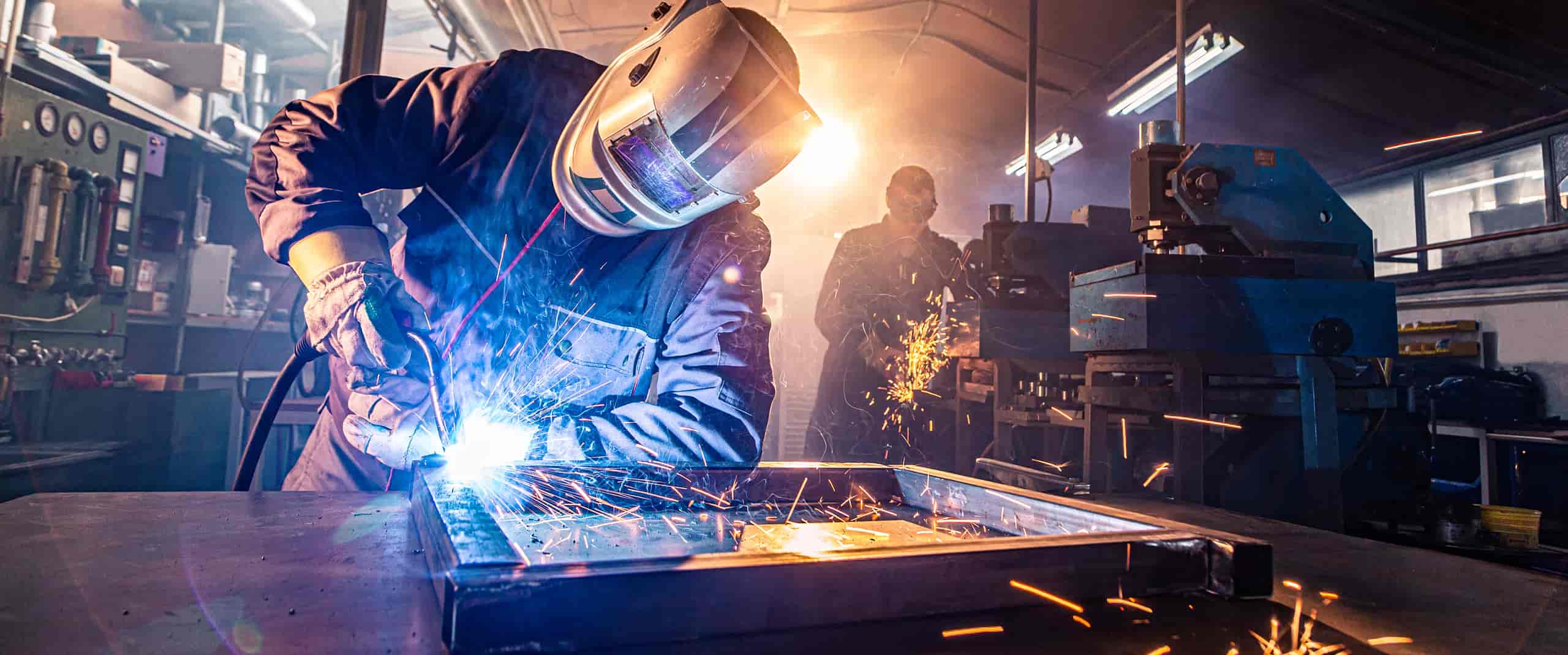
Crucial Element of WPS
Going over the integral parts of a welding treatment requirements (WPS) is vital for comprehending its function in welding procedures. One crucial aspect of a WPS is the welding procedure requirements, which outlines the specific welding processes to be made use of, such as gas tungsten arc welding (GTAW) or protected steel arc welding (SMAW) By including these key elements into the WPS, welding procedures can be standardized, making certain high quality, effectiveness, and safety in welding operations.
Methods for WPS Optimization
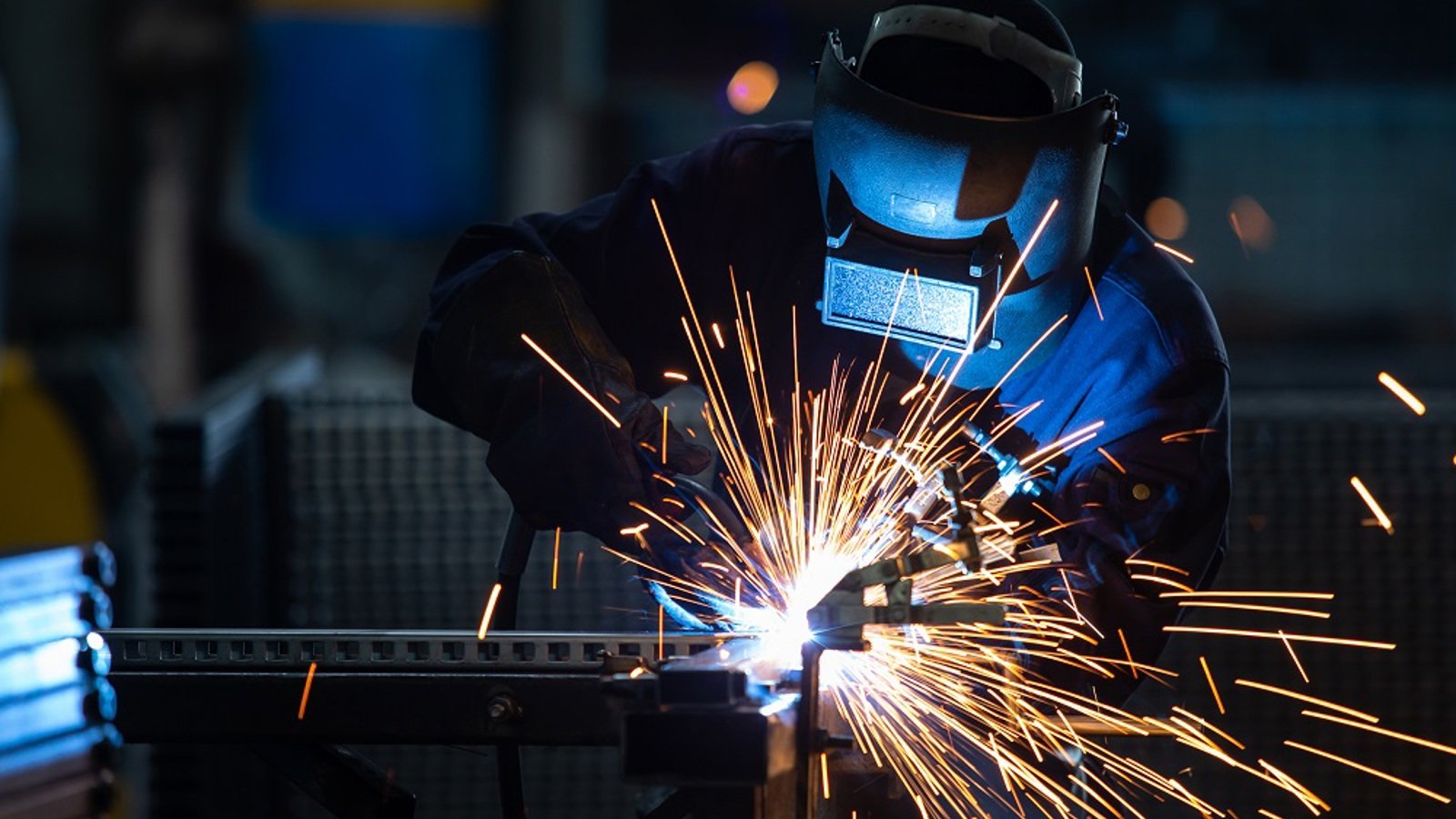
Second of all, training and credentials of welding personnel according to the certain needs of the WPS is critical. Giving detailed training programs and guaranteeing that welders are certified to perform procedures described in the WPS can bring about greater high quality welds and lowered rework.
Additionally, leveraging innovation such as welding software and monitoring systems can help in enhancing WPS. These devices can aid in monitoring variables, making certain specifications are within defined limits, and giving real-time comments to welders, allowing them to make immediate modifications for enhanced weld quality.
Typical Difficulties and Solutions
Facing challenges in executing the approaches for WPS optimization can prevent welding procedures' effectiveness and top quality. One typical difficulty is inadequate training or understanding of the welding procedure specs (WPS) among the welding team. This can cause inappropriate execution of welds, leading to problems original site and rework. To address this, comprehensive training programs ought to be implemented to ensure that all welders excel in using and interpreting WPS precisely.
One more difficulty is the lack of proper documentation and record-keeping, which is crucial for WPS optimization. Without clear records of welding parameters, products made use of, and evaluation outcomes, it ends up being challenging to recognize locations for renovation and make certain consistency in welding processes. Implementing a robust paperwork system, such as digital welding monitoring software, can aid improve record-keeping and promote data evaluation for constant enhancement.
Furthermore, inconsistent welding devices calibration and maintenance can present a substantial challenge to WPS optimization. Routine tools checks, calibration, and upkeep schedules ought to be stuck to purely to guarantee that welding specifications are properly managed and kept within the specified resistances (welding WPS). By dealing with these common difficulties with aggressive remedies, welding procedures can enhance effectiveness, quality, and total welding quality
Ideal Practices for WPS Implementation
To guarantee effective WPS implementation in welding procedures, adherence to sector standards and precise interest to information are critical. When starting WPS execution, it is important to begin by completely understanding the particular welding demands of the task. This involves a detailed evaluation of the welding procedure requirements, products to be bonded, and the environmental conditions in which the welding will certainly take location.
When the requirements are clear, the next step is to choose the appropriate welding treatment that straightens with these requirements. This includes seeking advice from the pertinent codes and requirements, such as those provided by the American Welding Society (AWS) or the International Company for Standardization (ISO), to make certain compliance and quality.
Moreover, recording the entire WPS execution procedure is vital for traceability and quality control. Detailed records ought to be maintained relating to welding specifications, product prep work, preheat and interpass temperature levels, welding consumables made use of, and any kind of deviations from the original procedure. Normal audits and evaluations of the WPS can help recognize locations for enhancement and ensure continuous optimization of the welding procedure.
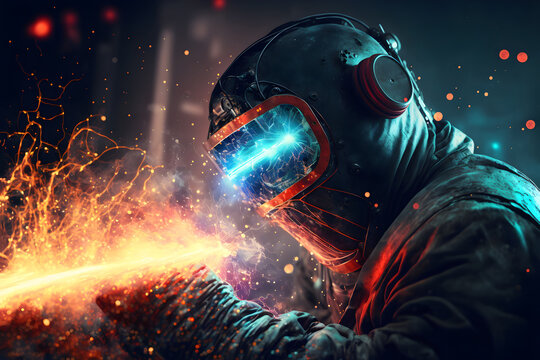

Verdict
In verdict, the implementation and optimization of Welding Procedure Specs (WPS) is vital for achieving welding excellence. By recognizing the vital elements of WPS, carrying out effective techniques for optimization, attending to common difficulties, and adhering to best techniques, welders can guarantee high-quality welds and secure working conditions. It is critical for professionals in the welding market to prioritize the appropriate application of WPS to improve general welding efficiency and attain preferred results.
The Importance of Welding Procedure Specs (WPS) in the welding market can not be overstated, serving as the backbone for making sure consistency, quality, and security in welding operations. A WPS supplies comprehensive guidelines on how welding is to go to my blog be lugged out, consisting of crucial variables such as materials, welding processes, joint design, filler steels, preheat and interpass temperatures, welding currents, Extra resources voltages, travel rates, and much more. One vital element of a WPS is the welding process requirements, which describes the specific welding processes to be utilized, such as gas tungsten arc welding (GTAW) or protected steel arc welding (SMAW) By incorporating these essential aspects right into the WPS, welding procedures can be standard, ensuring quality, performance, and safety in welding procedures.
It is critical for professionals in the welding sector to prioritize the appropriate application of WPS to improve overall welding efficiency and attain preferred end results.
Report this page